Last year, we posted a commentary and an update about a high energy arc fault (HEAF) event that occurred at the Turkey Point nuclear plant in Florida. The update included color photographs obtained from the Nuclear Regulatory Commission (NRC) via a Freedom of Information Act request showing the damage wrought by the explosion and ensuing fire. Neither the HEAF event or its extensive damage surprised the NRC—they had been researching this fire hazard for several years. While the NRC has long known about this fire hazard, its resolution remains unknown. Meanwhile, Americans are protected from this hazard by an IOU. The sooner this IOU is closed out, the better that Americans in jeopardy will be really and truly protected.
What is a HEAF?
The Nuclear Energy Agency (NEA), which has coordinated international HEAF research efforts for several years, defines HEAF this way: “An arc is a very intense abnormal discharge of electrons between two electrodes that are carrying an electrical current. Since arcing is not usually a desirable occurrence, it is described as an arcing fault.”
Nuclear power plants generate electricity and use electricity to power in-plant equipment. The electricity flows through cables or metal bars, called buses. An arc occurs when electricity jumps off the intended pathway to a nearby metal cabinet or tray.
Electricity is provided at different voltages or energy levels for different needs. Home and office receptacles provide 120-volt current. Nuclear power plants commonly have higher voltage electrical circuits carrying 480-volt, 4,160-volt, and 6,900-volt current for motors of different sizes. And while main generators at nuclear plants typically produced electricity at 22,000 volts, onsite transformers step up the voltage to 345,000 volts or higher for more efficient flow along the transmission lines of the offsite power grid.
How is the Risk from HEAF Events Managed?
Consistent with the overall defense-in-depth approach to nuclear safety, HEAF events are managed by measures intended to prevent their occurrence backed by additional measures intended to minimize consequences should they occur.
Preventative measures include restrictions on handling of electrical cables during installation. Limits on how much cables can be bent and twisted, and on forces applied when cables are pulled through wall penetrations seek to keep cable insulation intact as a barrier against arcs. Other preventative measures seek to limit the duration of the arc through detection of the fault and automatic opening of a breaker to stop the flow of electrical current through the cables (essentially turning the arc off).
Mitigative measures include establishing zones of influence (ZOI) around energized equipment that controls the amount of damage resulting from a HEAF event. Figure 1 illustrates this concept using an electrical cabinet as the example Electrical cabinets are metal boxes containing breakers, relays, and other electrical control devices. Current fire protection regulatory requirements impose a 3-foot ZOI around electrical cabinets and an 18-inch ZOI above them. Anything within the cabinet and associated ZOI is assumed to be damaged by the energy released during a HEAF event. Sufficient equipment must be located outside the affected cabinet and its ZOI to survive the event and adequately cool the reactor core to prevent meltdown.

Fig. 1 (Source: Nuclear Regulatory Commission)
Even with these preventative and mitigative measures, NEA recognized the hazard that HEAF events poses when it wrote in a May 2017 report: “The electrical disturbance initiating the HEAF often causes loss of essential electrical power and the physical damage and products of combustion provide significant challenges to the operators and fire brigade members handling the emergency. It is clear that HEAFs present one of the most risk significant and challenging fire scenarios that a [nuclear power plant] will face.”
What is the Problem with HEAF Risk Management?
Actual HEAF events have shown that the preventative and mitigative measures intended to manage the hazard have shortcomings and weaknesses. For example, arcs have sometimes remained energized far longer than assumed, enabling the errant electricity to wreak more havoc.
Additionally, HEAF events have damaged components far outside the assumed zones of influence, such as in the Turkey Point event from March 2017. In other words, the HEAF hazard is larger than its defenses.
How is the HEAF Risk Management Problem Being Resolved?
On March 11, 2011, an earthquake offshore of Japan and the tsunami it spawned led to the meltdown of three reactors at the Fukushima Daiichi nuclear plant. That earthquake also caused a HEAF event at the Onagawa nuclear plant in Japan. The ground motion from the earthquake prevented an electrical circuit breaker from opening to limit the duration of the arc. The HEAF event damaged equipment and started a fire (Fig. 2). Because the fire brigade could not enter the room due to heat and smoke, the fire blazed for seven hours until it had consumed all available fuel. As an NRC fire protection engineer commented in April 2018, “If Fukushima wasn’t occurring, this is probably what would have been in the news headlines.” Onogawa was bad. Fukushima was just worse.
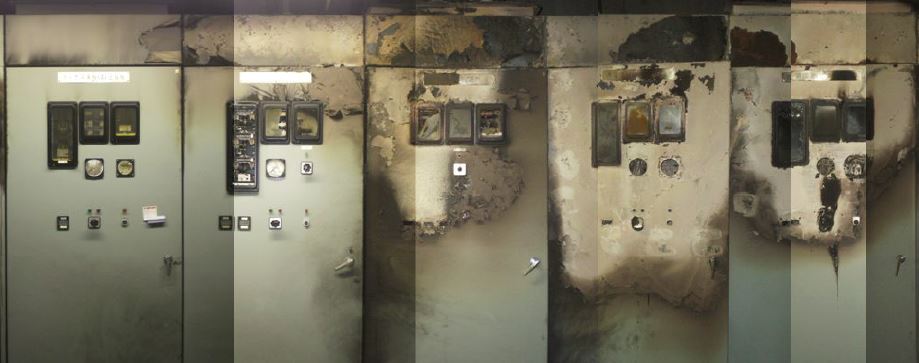
Fig. 2 (Source: Nuclear Regulatory Commission)
Research initiated in Japan following the Onagawa HEAF event sought to define the factors affecting the severity of the events. Because the problem was not confined to nuclear power plants in Japan, other countries collaborated with the Japanese researchers in pursuit of a better understanding of, and better protection for, HEAF events.
The NRC participated in a series of 26 tests conducted between 2014 and 2016 using different types of electrical panels, bus bar materials, arc durations, electrical current voltages, and other factors. The results from the tests enabled the NRC to take two steps.
First, the NRC entered HEAF events into the agency’s generic issues program in August 2017. In a related second step, the NRC formally made the owners of all operating US nuclear power plants aware of this testing program and its results via an information notice also issued in August 2017. The NRC has additionally shared its HEAF information with plant owners during the past three Regulatory Information Conferences and several other public meetings and workshops.
The NRC plans a second series of tests to more fully define the conditions that contribute to the severity of HEAF events.
How Are HEAF Events Tested?
Test 23 during the Phase I program subjected a 480-volt electrical cabinet with aluminum bus material to an arc lasting 7.196 seconds. Figure 3 shows the electrical cabinet with its panel doors opened prior to the test. A pointer on the left side of the picture shows the location where the arc was intentionally caused.
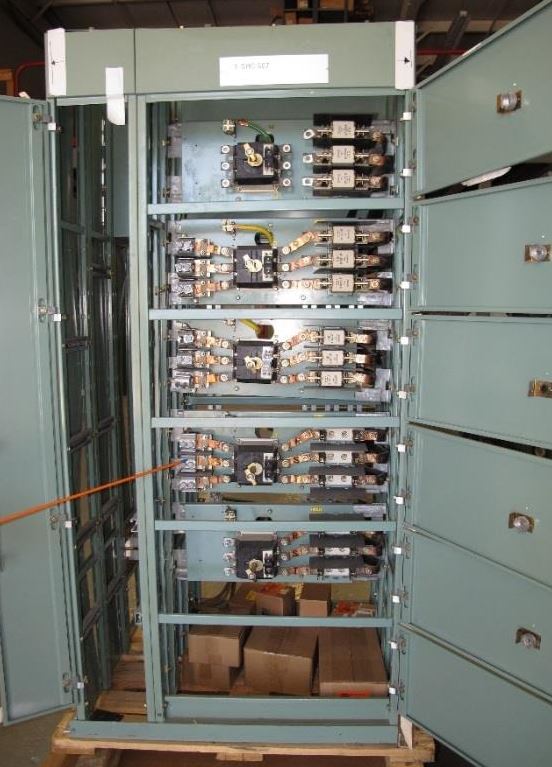
Fig. 3 (Source: Nuclear Energy Agency)
To induce an arc for the test, a wire was wrapped around all three phases of the 480-volt alternating current connectors within one of the cabinet’s panels as shown in Figure 4. On the right edge of the picture is a handswitch used to connect or disconnect electrical power flowing into the cabinet via these buses to in-plant electrical loads.

Fig. 4 (Source: Nuclear Energy Agency)
Instrumentation racks and cameras were positioned around the cabinet being tested. The racks included instruments measuring the temperature and pressure radiating from the cabinet during the HEAF event. High-speed, high definition cameras recorded the progression of the event while infrared cameras captured its thermal signature. A ventilation hood positioned over the cabinet connected to a duct with an exhaust fan conducted smoke away from the area to help the cameras see what was happening. More importantly, the ventilation duct contained instruments measuring the heat energy and byproducts released during the event.

Fig. 5 (Source: Nuclear Regulatory Commission)
What Are the HEAF Test Results?
For a DVD containing reports on the HEAF testing conducted between 2014 and 2016 as well as videos from the 26 tests conducted during that period, send an email with your name and address to RES_DRA_FRBQnrc.gov. Much of the information in this commentary comes from materials on the DVD the NRC mailed me in response to my request.
Test 4 in the Phase I Program subjected a 480-volt electrical cabinet with aluminum bus material to an arc lasting only 0.009 seconds (i.e., 9 milliseconds). The short duration arc had minimal consequences, entirely missed if one blinks at the wrong time while watching the video. This HEAF event did not damage components within the electrical cabinet, yet alone any components outside the 3-foot zone of influence around it.
Test 3 in the Phase I Program subjected a 480-volt electrical cabinet with copper bus material to an arc lasting 8.138 seconds. The longer duration arc produced greater consequences than in Test 4. But the video shows that the consequences are largely confined to the cabinet and zone of influence.
Test 23 in the Phase I Program subjected a 480-volt electrical cabinet with aluminum bus material to an arc lasting 7.196 seconds. The voltage level and arc duration for Test 23 were essentially identical to that for Test 3, but the consequences were significantly different. Aluminum behaved differently than copper during the HEAF event, essentially fueling the explosion and ensuing fire. As a result, the damage within the cabinet, zone of influence, and even beyond the 3-foot zone of influence was much greater. For example, some of the instruments on the rack positioned just outside the 3-foot zone of influence were vaporized.
Until debris from the event obscured the lens of a camera positioned many feet outside the 3-foot zone of influence, a side view of the Test 23 HEAF event showed it was a bigger and badder event than the HEAF event in Test 3 and the HEAF event in Test 4.
Figure 6 shows the electrical cabinet with its panel doors open after Test 23. The cabinet clearly looks different from its pre-test appearance (see Figure 4). But this view does not tell the entire story.

Fig. 6 (Source: Nuclear Energy Agency)
Figure 7 shows the left side of the electrical cabinet after Test 23. The rear upper left corner of the cabinet is missing. It was burned and/or blown away by the HEAF event. The cabinet is made of metal, not wood, plastic, or ice. The missing cabinet corner is compelling testimony to the energy released during HEAF events.
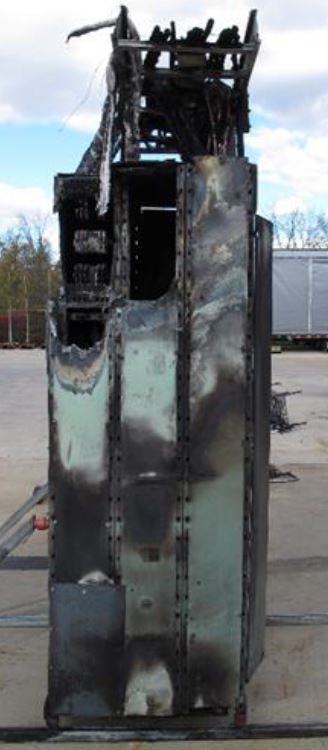
Fig. 7 (Source: Nuclear Energy Agency
Tests 3, 4 and 23 all featured electrical cabinets supplied with 480-volt power.
Tests 4 and 23 each featured aluminum bus material. Test 4 had negligible consequences while Test 23 had significant consequences, attesting to the role played by arc duration. The arc lasted 0.009 seconds in Test 4 while it lasted 7.196 seconds in Test 23.
Tests 3 and 23 featured arcs lasting approximately 8 seconds. Test 23 caused substantially greater damage within the electrical cabinet and beyond the 3-foot zone of influence due to the presence of aluminum rather than copper materials.
How Vulnerable Are US Nuclear Plants to HEAF Events?
The Phase I series of tests revealed that HEAF events depend on the voltage level, the conducting material (i.e., copper, iron, or aluminum), and the arc duration. The higher the voltage, the greater the amount of aluminum, and the longer the arc duration, the greater the consequences from HEAF events.
The NRC received results in 2017 from an industry survey of US nuclear plants. The survey showed that the plants have electrical circuits with voltage levels of 480, 4160, 6900, and 22000 volts. The survey also showed that while some plants did not have electrical circuits with components plated with aluminum, many did.
As to arc durations, actual HEAF events at US plants have involved arc durations longer than the 8 seconds used in Tests 3 and 23. The May 2000 event at Diablo Canyon lasted 11 seconds. The March 2010 event at HB Robinson last 8 to 12 seconds. And the June 2011 event at Fort Calhoun last 42 seconds and likely would have lasted even longer had operators not intervened by manually opening an electrical breaker to end the event.
So, many US nuclear plants have all the ingredients necessary for really nasty HEAF events.
What Might the Fixes Entail?
The testing program results to date suggest a tiered approach to the HEAF event solution. Once the key factors (i.e., combinations of voltage levels, materials, and arc durations) are definitively established, they can be used to screen out configurations within the plant where a HEAF event cannot compromise safety margins. For example, a high voltage electrical cabinet with aluminum bus material and suspect arc duration limiters might need no remedies if it is located sufficiently far away from safety components that its HEAF vaporization carries only economic rather than safety implications. Similarly, configurations with voltage levels and materials that remain bound by the current assumptions like the 3-foot zone of influence would require no remedies.
When a configuration cannot be screened out, the remedy might vary. In some cases, it might involve providing more reliable, quick-acting fault detection and isolation systems that limit the duration of the arc. In other cases, replacing aluminum buses with copper or iron buses might be a suitable remedy. And the fix might be simply installing a protective wall between an electrical cabinet and safety equipment.
Further HEAF testing will expand knowledge of the problem, thus more fully informing the decisions about effective solutions.
UCS Perspective
It has been known for many years now that HEAF events could cause wider damage than currently assumed in designing and applying fire protection measures. As a result, a fire could damage primary safety systems and their backups—the very outcome the fire protection regulatory requirements are intended to prevent.
This is normally the time and spot where I chastise the NRC for dragging its feet in resolving this known safety hazard. But while years have passed since the HEAF hazard flag was first raised, the NRC’s feet have been busy. For while it was known that HEAF events could cause greater damage than previously realized, it was not known what factors played what roles in determining the severity of HEAF events and the damage they inflict. The NRC joined regulatory counterparts worldwide in efforts designed to fill in these information gaps. That knowledge was vitally needed to ensure that a real fix, rather than an ineffective band-aid fix, was applied.
That research took time to plan and conduct. And further research is needed to fully define the problem to find its proper solution. In the meantime, the NRC has been very forthcoming with plant owners and the public about its concerns and associated learnings to date.
While the NRC’s efforts to better understand HEAF events may be justified, it’s worth remembering that the agency’s intentions and plans are little more than IOUs to the millions of Americans living close to vulnerable nuclear plants. IOUs provide zero protection. The NRC needs to wrap up its studies ASAP and turn the IOUs into genuine protection.