As electric vehicle (EV) sales continue to increase, questions about how these cars and their batteries will be disposed of have been top of mind for current owners, future buyers, policymakers, and many experts in the automotive industry.
EVs are a newer technology, and their batteries require different end-of-life processing than gasoline vehicles. Luckily, lithium-ion battery recycling research and development has been going on for years and there is an existing and growing repurposing and recycling system in North America for these components. The map below is from recent research that explores the network of companies already recycling and repurposing batteries – these include recycling companies such as Redwood Materials, Li-Cycle, and Ascend Elements. The industry is quickly growing capacity for future recycling, with planned facilities in Nevada, New York, and Georgia, to name just a few.
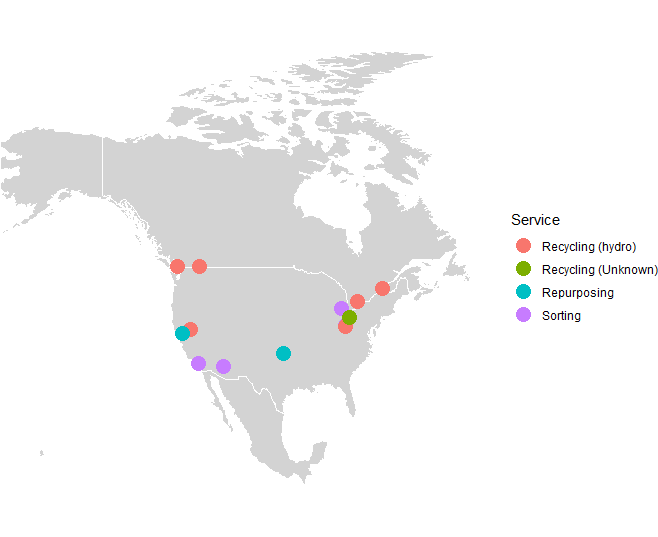
Current lithium-ion battery collection, repurposing, and recycling network in North America.
Slattery et al. (2021).
First reused and repurposed, then recycled
After a battery’s first life in a car and before it is recycled, it can be reused, refurbished, and repurposed.
If the battery isn’t damaged during its use in an EV, such as in a car accident, these batteries have additional usable capacity – an estimated 80% of the original rated capacity. This means that if the battery was manufactured to store 100 kWh, it can now store up to 80 kWh. In order to make use of the remaining capacity, the batteries can be broken down to salvage smaller components for reuse and refurbishment, or they can be repurposed and used in a less demanding application, such as stationary storage.
For stationary storage, companies such as RePurpose Energy and B2U Storage Solutions are repurposing these batteries to be used for renewable energy generation support. They connect multiple EV batteries together, along with battery monitoring and cooling technology, to create a larger battery that is about the size of a shipping container. The battery stores solar electricity generated during the day and supplies electricity at high-demand times in the evening. As the grid becomes cleaner, added grid storage becomes more necessary to support the generation variability of renewable sources. These used batteries are a great way to both extend the lifespan of a product that has already been manufactured and support the renewable energy transition. After this second-life use, the batteries are then ready to be recycled.
What’s valuable in a vehicle battery?
Lithium-ion batteries contain many valuable materials worth recovering and saving from a landfill.
Prior to recycling, the battery is disassembled and shredded using large machinery, breaking the battery into small pieces. Once the shredding is completed, the materials are sifted and separated based on size. This divides them into three different categories: plastics, ferrous materials, and non-ferrous materials (also called black mass). The black mass consists of the critical materials, cobalt, lithium, nickel, and manganese, which can individually be recovered using a hydrometallurgical process.
Hydrometallurgical recycling begins with leaching to create a solvent that contains the critical materials. The individual materials are then recovered using solvent extraction, precipitation, and purification. Hydrometallurgy is well known in the metals industry as a similar process is also used to extract the materials from ore after it is mined. Many US-based lithium-ion recycling companies use a variation of this process and report a material recovery rate of 95%–98%.
Can we use recycled materials to manufacture new batteries?
Yes! Once materials have been recovered, they can then be processed and used in the manufacturing of new lithium-ion batteries. This is a preferable source to using virgin ore because it reduces the amount of mining necessary to produce EVs.
Recent research has shown that by 2050 recycled materials could supply 45–52% of cobalt, 22–27% of lithium, and 40–46% of nickel used in the United States light- and heavy-duty vehicle fleet. Efforts across the United States to increase the sales of EVs are underway – places like California expect to have 100% of all car sales be electric by 2035 – so being able to recycle batteries and reuse the metal within them is a critical step in the transformation to a cleaner transportation system.
Recycling is key to making EVs greener
EV batteries currently represent about half of the lithium-ion batteries (by mass) that are being recycled, which also includes consumer electronics and waste from battery manufacturing. With 3.8 million EVs on the road today in North America and sales growing year over year, the number of EVs retiring in coming years will continue to increase as they eventually are totaled or age out of the fleet.
This increase will result in vehicle batteries comprising a much higher percentage of the recycling stream; retirements are expected to be 6 to 7 times higher in 2025 than in 2020 and 20 to 40 times higher in 2030. Companies recycling these batteries are setting themselves up to accommodate this upcoming wave by expanding their capacity.
These recycling companies are securing a battery stream by partnering with auto manufacturers. For example, major automakers are partnering with Redwood Materials, a recycling company based in Nevada. Redwood is not only recycling but will soon be closing the material loop by manufacturing battery components with recovered materials.
Redwood Materials has also implemented a recycling program to learn more about the location of retired and uncollected batteries, and how to decrease the costs of transporting these batteries to the recycling facility. Transportation from their location of retirement to the recycling plant is expensive, representing about 50-60% of the recycling costs. These costs are due to the special packaging and requirements needed for shipping retired batteries and their large size and weight. But, transportation costs can potentially be decreased if a more efficient collection system is developed.
Researchers have been modeling potential reverse logistics networks and now Redwood Materials is completing research of their own through a learning-by-doing approach. Their new Recycling Program consists of picking up and recycling any retired lithium-ion battery in California at no cost. They are also working with dealerships and dismantlers in order to collect as many batteries as possible.
California is considering battery recycling requirements
As you can see, there is a lot happening in the industry space. And while there is currently no recycling requirement in the United States, California passed a bill that indicates recycling may be a priority for the state.
Assembly Bill 2832 passed in 2018 creating the California Battery Recycling Advisory Group. This group consists of automotive and battery manufacturers, government agency representatives, and public interest groups. They recently recommended policies to the legislature that could increase the recycling of EV batteries. These recommendations included the creation of a California State requirement that batteries be recycled, holding the auto manufacturer responsible for ensuring that happens. This is not unlike how mattress, paint, and carpet disposal is currently regulated within California.
In addition to the California work, the federal government is also paying attention. In the Bipartisan Infrastructure Bill, funds were allocated toward battery recycling research and development. This is in addition to the funding of the ReCell Center, a lab created by the Department of Energy that is focused on decreasing costs and increasing yields of recycling.
Battery end-of-life is very important for ensuring that batteries are safely disposed of and that materials are recovered and used again in battery manufacturing. While there is a lot going on to push forward the uptake of EVs and replace gasoline cars for good, many people are simultaneously working to make sure that EV batteries are being reused, repurposed, and recycled.