Disaster by Design/Safety by Intent #29
Disaster by Design
Disaster by Design/Safety by Intent #26 described a progression leading to overheating and damage to a reactor core, often labeled a meltdown. Disaster by Design/Safety by Intent #27 described the damage to a reactor core that can result from reactivity excursions. Disaster by Design/Safety by Intent #28 and #29 mirror those commentaries by describing how irradiated fuel stored in spent fuel pools can experience damage from overheating and reactivity excursions.
The Nuclear Regulatory Commission’s expectations for safely storing spent fuel are spelled out in Section 9.1.2 of the agency’s Standard Review Plan for nuclear power plants. Protection against reactivity excursions in the spent fuel pool are mandated by 10 CFR 50.68, Criticality Accident Requirements.
Criticality occurs when fissionable material (i.e., uranium and plutonium) achieves a nuclear chain reaction. The splitting, or fissioning, of certain uranium and plutonium atoms releases energy and subatomic particles called neutrons. The energy powers the plant. The neutrons sustain the nuclear chain reaction by interacting with other uranium and plutonium atoms to cause more fissions.
A term called K-effective, K-eff for short, tracks the population of released neutrons that cause fissions. When the reactor has a nuclear chain reaction that is neither increasing or decreasing (in other words, at steady state operation), K-eff is 1.0 reflecting that the number of neutrons now is the same as the number from five minutes ago. When the number of neutrons now exceeds the number from five minutes ago, K-eff is greater than 1.0. When the number of neutrons now is less than the number from five minutes ago, K-eff is less than 1.0. The NRC’s regulations require that spent fuel be stored such that K-eff is 0.95 or less.
Spent Fuel Pool Storage Racks
Spent fuel pools have walls and a floor made from reinforced concrete. Spent fuel assemblies reside in metal storage racks within the pools. Fig. 1 suggests a single storage rack is installed in each spent fuel pool. In reality, multiple storage racks are used.

Fig. 1 (Source: NRC)
Each storage rack is made from metal (Fig. 2). Each rack has feet allowing a few inches of clearance between the floor of the spent fuel pool and the bottom of the rack to allow water to flow under the rack and upward passed the irradiated fuel assemblies.
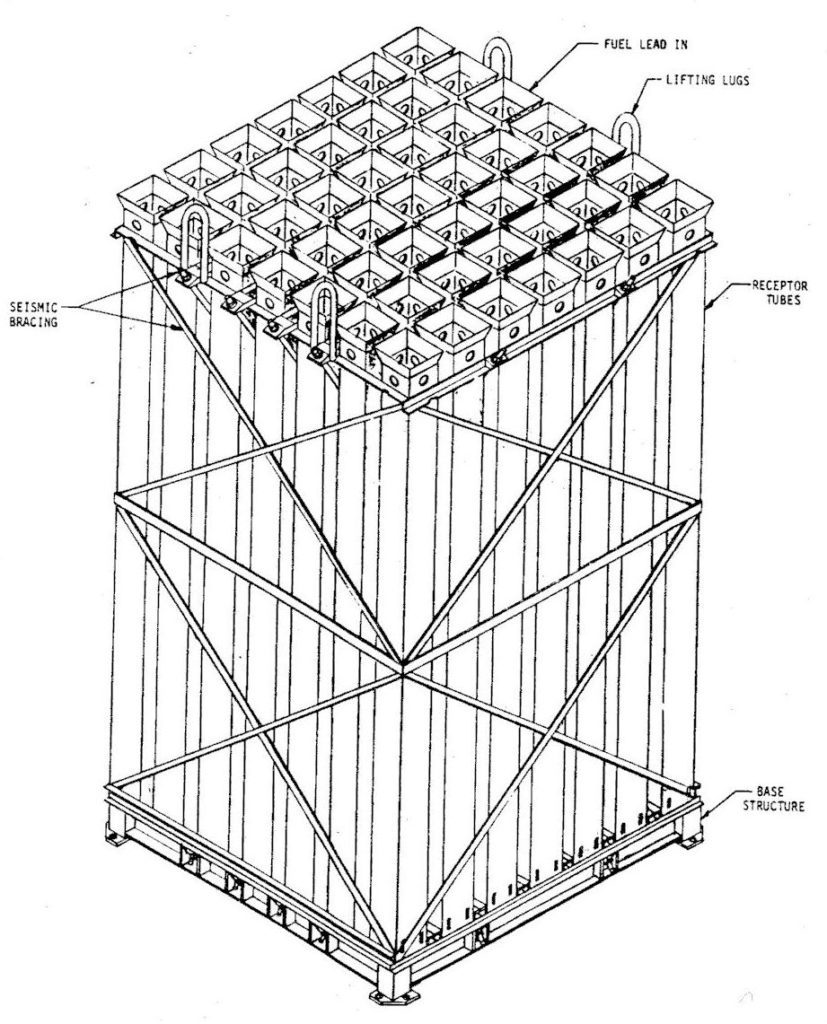
Fig. 2 (Source: NRC)
Early nuclear power plants had what have been called low-density storage racks. In this typical configuration, the 14 racks could hold up to 280 fuel assemblies in 14 rows and 20 columns (Fig. 3). The sheer spacing between fuel assemblies in adjacent storage locations was sufficient to prevent K-eff from exceeding 0.95. A spent fuel pool criticality could not occur because the racks’ geometry precluded fuel assemblies from being stored close enough to form a critical mass.
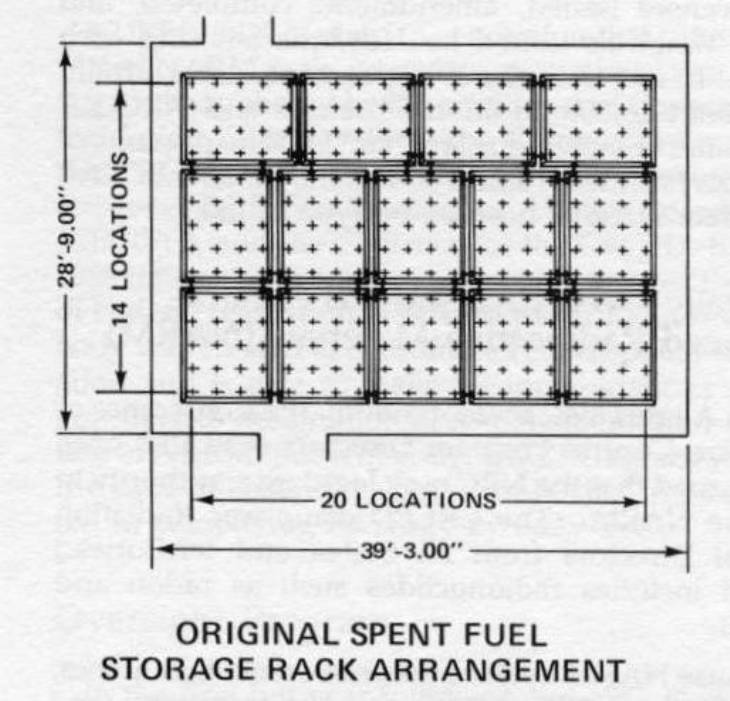
Fig. 3 (Source: NRC)
When the federal government banned reprocessing of spent fuel and failed to provide a repository for spent fuel disposal, spent fuel had no place to go. To accommodate the significantly larger inventory of spent fuel that was forced to remain onsite due to the federal government’s failing, early nuclear power plants reracked their spent fuel pools with what have been called high-density storage racks (Fig. 4). “Newer” plants (those that went into service in the mid-1980s and 1990s) also installed high-density storage racks.
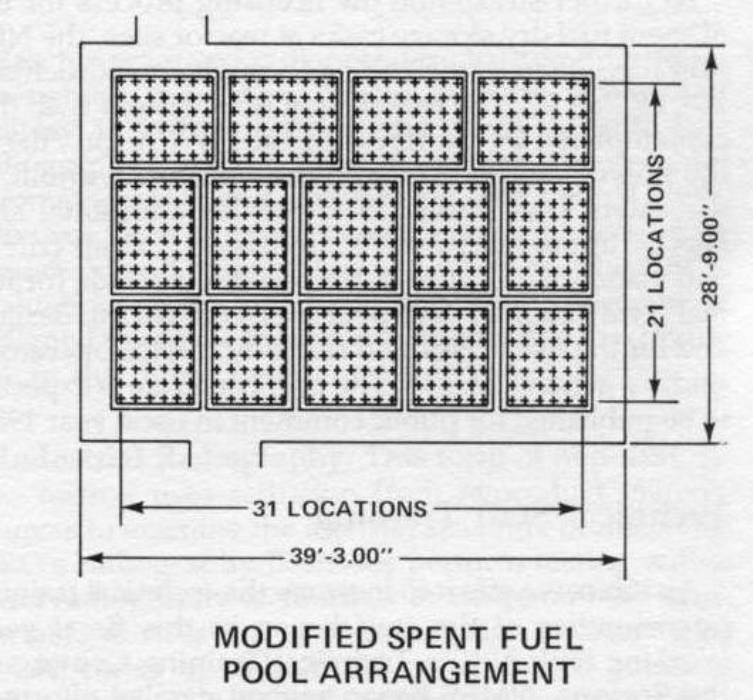
Fig. 4 (Source: NRC)
The diagram shows how 14 high-density racks placed into the same 39 feet, 3 inches by 28 feet, 9 inches spent fuel pool can hold up to 651 fuel assemblies in 21 rows and 31 columns. Simply by storing fuel assemblies closer together—closer than they are packed within a reactor core—the high density racks can store more than double the inventory in the same space.
But geometry is no longer an ally against spent fuel pool criticality. The close confines could let K-eff not only exceed 0.95, but to also rise above 1.0 to cause a reactivity excursion.
To comply with the NRC’s regulations, spent fuel pools equipped with high-density storage racks substitute neutron absorbing materials for geometry. Boron is a commonly used neutron absorber. Boron is like “neutron glue” because it has a very strong affinity for neutrons. Neutrons captured by boron atoms cannot interact with uranium and plutonium atoms and cause fissions. Using “neutron glue” can keep K-eff from exceeding 0.95, thus complying with the anti-criticality regulation.
Neutron-absorbing material, like boron, can be dissolved into the spent fuel pool water. There are safety and economic drawbacks of this option. On the safety side, it introduces the risk of criticality when regular water is used to re-fill a pool following an accident that partially drains it. On the financial side, it incurs the cost of having to continually monitor the chemistry of the spent fuel pool water and periodically make adjustments to maintain the proper concentration of neutron-absorber.
Neutron-absorbing material can also be integrated into spent fuel pool storage racks during manufacturing. For example, one vendor sandwiched neutron-absorbing material in the form of a plastic sheet between the thin metal walls of the racks. This option also had safety and economic drawbacks. If the metal walls of the sandwich gapped, the neutron-absorbing material inside could sag or droop. In addition, the neutron-absorbing material could leach through tiny cracks in the metal and get carried away by the water. The financial consequences of this option include the cost of periodic testing conducted to determine whether the neutron-absorbing material is still where it is supposed to be in the needed amounts.
“Neutron glue” has proven to be considerably less reliable than geometry in protecting against spent fuel pool criticality. The NRC issued Generic Letter 2016-01 on April 7, 2016, to nuclear plant owners asking them to answer five essay questions:
- What neutron-absorbing material is credited in criticality studies and how is this material configured in the spent fuel pool?
- What monitoring program is used to confirm that the neutron-absorbing material is fulfilling its credited safety role?
- What is the technical basis for the frequency of the monitoring program’s efforts?
- How is the neutron-absorbing material modeled in the criticality studies?
- What is the technical basis for concluding that the neutron-absorbing material will continue to perform its credited safety role during design basis accidents?
Chinks in the Protective Armor
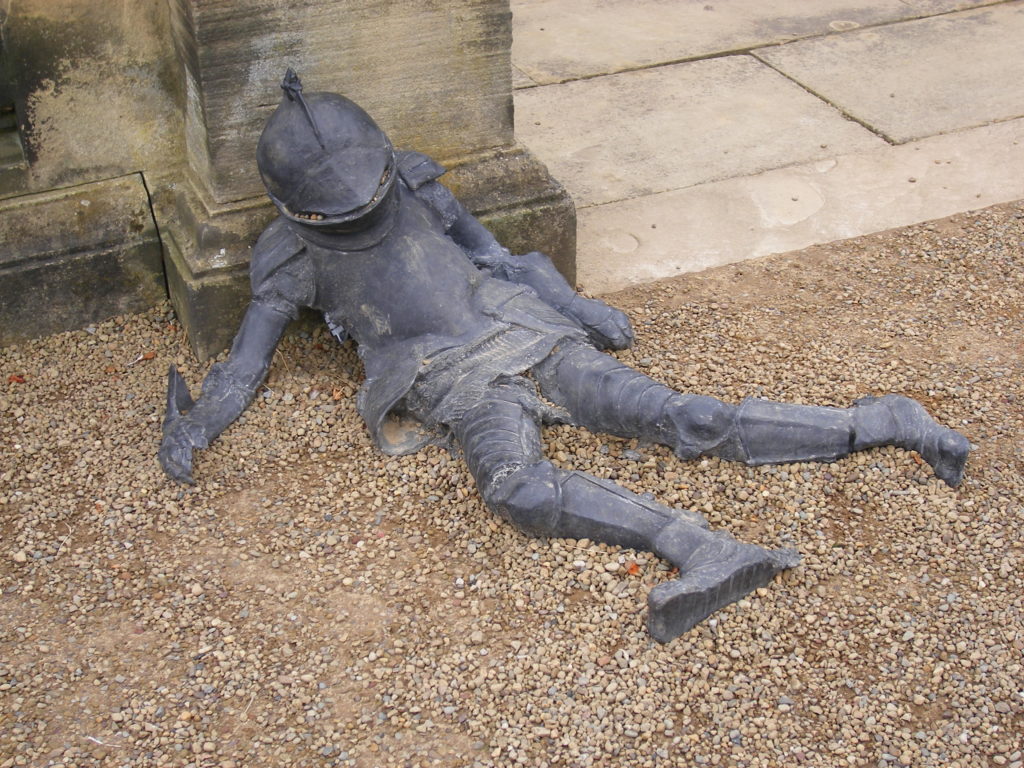
(Source: Elliott Brown)
There have been many problems with neutron-absorbing materials in spent fuel pools at many plants spanning many years. Only a representative sampling of the problems will be described here to prevent this blog from becoming a blogopedia.
Indian Point (NY) 2012: Workers mistakenly loaded 11 new fuel assemblies into the wrong locations within the spent fuel pool storage racks. The criticality measures required that new fuel assemblies not be stored so close together, but the administrative controls designed to prevent improper loading failed.
Zion (IL) 2011: The spent fuel pool shared by the Unit 1 and 2 reactors featured a two-region configuration. All spent fuel assemblies could be stored in one region while only those spent fuel assemblies meeting certain criteria could be stored in the second region. Workers found several spent fuel rods mistakenly stored in a region that violated the criticality prevention requirements.
Peach Bottom (PA) 2010: Workers used a computer code to model the consequences from degradation of neutron-absorbing materials within the spent fuel pool storage racks. But NRC inspectors determined that they had not accurately modeled the degradation rate and had used several non-conservative assumptions. When workers corrected these deficiencies, the re-analysis revealed that several storage locations violated regulatory requirements. Irradiated fuel assemblies were relocated to other storage rack locations and administrative controls were developed to prevent loading fuel assemblies into several “bad” storage rack locations.
Turkey Point (FL) 2010: The NRC fined the owner of Turkey Point $70,000 in 2010 for three violations with neutron-absorbing material inserted into spent fuel pool storage racks.
Oconee (SC) 2009: The company informed the NRC that they had violated requirements governing errors when placing fuel assemblies in the spent fuel pool shared by the Unit 1 and 2 reactors on three occasions. They were supposed to immediately correct errors, but had allowed the errors to remain in place between one week and one month.
Sequoyah (TN) 2009: While repositioning spent fuel assemblies within the spent fuel pool to better distribute the heat load, workers mistakenly stored four spent fuel assemblies in places not allowed by the criticality prevention requirements.
Palisades (MI) 2008: Workers discovered that degradation of Carborundum neutron-absorbing material in the spent fuel storage racks was so severe that only about one-third of the original material remained in place. Because workers did not routinely monitor the neutron-absorbing material, when the degradation began and how quickly it progressed could not be determined.
South Texas Project (TX) 1995: Workers determined that degradation of neutron-absorbing material sandwiched between the thin metal walls of spent fuel pool storage racks was so degraded that several locations could not be used without violating the criticality protection requirements.
Fort Calhoun (NE) 1994: Workers determined that nearly 60 percent of the neutron-absorbing material was missing from some spent fuel pool storage rack locations. The loss was attributed to exposure to high energy gamma rays that degraded the material.
Palisades (MI) 1993: After removing several metal samples containing neutron-absorbing material from the spent fuel pool, workers found that up to 90 percent of the material had been lost from some samples. The loss was attributed to exposure to high energy gamma rays in combination with exposure to water in the spent fuel pool.
Quad Cities (IL) 1987: The company informed the NRC about gaps they had detected in neutron-absorbing material sandwiched between the thin metal walls of spent fuel pool storage racks. The average gap size was 1.5 inches.
Maine Yankee (ME) 1982: After being unable to insert a fuel assembly into a spent fuel pool storage rack location, workers discovered that metal plates containing neutron-absorbing materials had swollen. The bulging plates blocked the insertion. Further investigation identified six locations loaded with irradiated fuel assemblies where the bulging plates hindered removal of the assemblies.
Safety by Intent
The NRC reviews spent fuel storage configurations to verify compliance with 10 CFR 50.68 and other safety regulations before issuing initial reactor operating licenses. The NRC reviews applications submitted by plant owners seeking to increase the maximum storage capacity in spent fuel pools before authorizing the increases.
How is it even remotely possible that the NRC would not already know the answers to the five questions listed above that it asked plant owners via Generic Letter 2016-01? The fact that the NRC seeks answers to these five questions implies that the agency lacked sufficient awareness and understanding when making these licensing decisions. “Safe as far as I know” is only acceptable when one has sufficient awareness and understanding.
Besides, the NRC is missing the best solution to this problem. Rather than expend untold resources and take another decade or so figuring out to keep neutron-absorbing materials where they are supposed to be, the NRC should implement the easy, low-tech fix—compel owners to accelerate the transfer of irradiated fuel assemblies from over-crowded spent fuel pools into dry storage.
About 75% of the nation’s irradiated fuel is currently stored in spent fuel pools. With technology already available and approved by the NRC, we could transfer irradiated fuel into dry storage such that only about 25% remained in the pools. This remaining inventory could be spread out in the pools to restore geometry as the reliable protection against spent fuel criticality.
Implementing this measure would resolve once and for all the longstanding neutron-absorbing material safety dilemma.
The NRC can wait until this longstanding problem someday causes harm, or it can pro-actively take steps that protect people and the environment consistent with the agency’s tag line proclaims.
—–
UCS’s Disaster by Design/ Safety by Intent series of blog posts is intended to help readers understand how a seemingly unrelated assortment of minor problems can coalesce to cause disaster and how effective defense-in-depth can lessen both the number of pre-existing problems and the chances they team up.