Electrifying our transportation system is essential for mitigating emissions that cause climate change and adverse health impacts. This electrification will require a lot more batteries and therefore a lot more minerals. Recovering these materials from retired electric vehicle (EV) batteries is an alternative source to mining. Essentially, the materials recovered through battery recycling can replace future material supply that would otherwise need to be extracted from the earth to meet demand.
Estimates show that in 2050, the United States can meet about half of EV demand for cobalt and nickel and a quarter of lithium with minerals recovered through recycling. While EVs already result in less greenhouse gas emissions than the gasoline alternative, using these recycled materials substantially lowers impacts associated with material sourcing.
Prior to recycling, the battery retired from use in an EV can be used in a second-life application. This means it is either reused in another vehicle or it is repurposed for use in a stationary storage application. Eventually, the battery will reach its end of life and should be recycled, recovering minerals to then go back into the battery manufacturing stream.
The circular process starts at manufacturing, flows to the first use in an EV, is repurposed for a second life, recycled, and then eventually the minerals are back to manufacturing. This is referred to as material circularity or the circular economy.
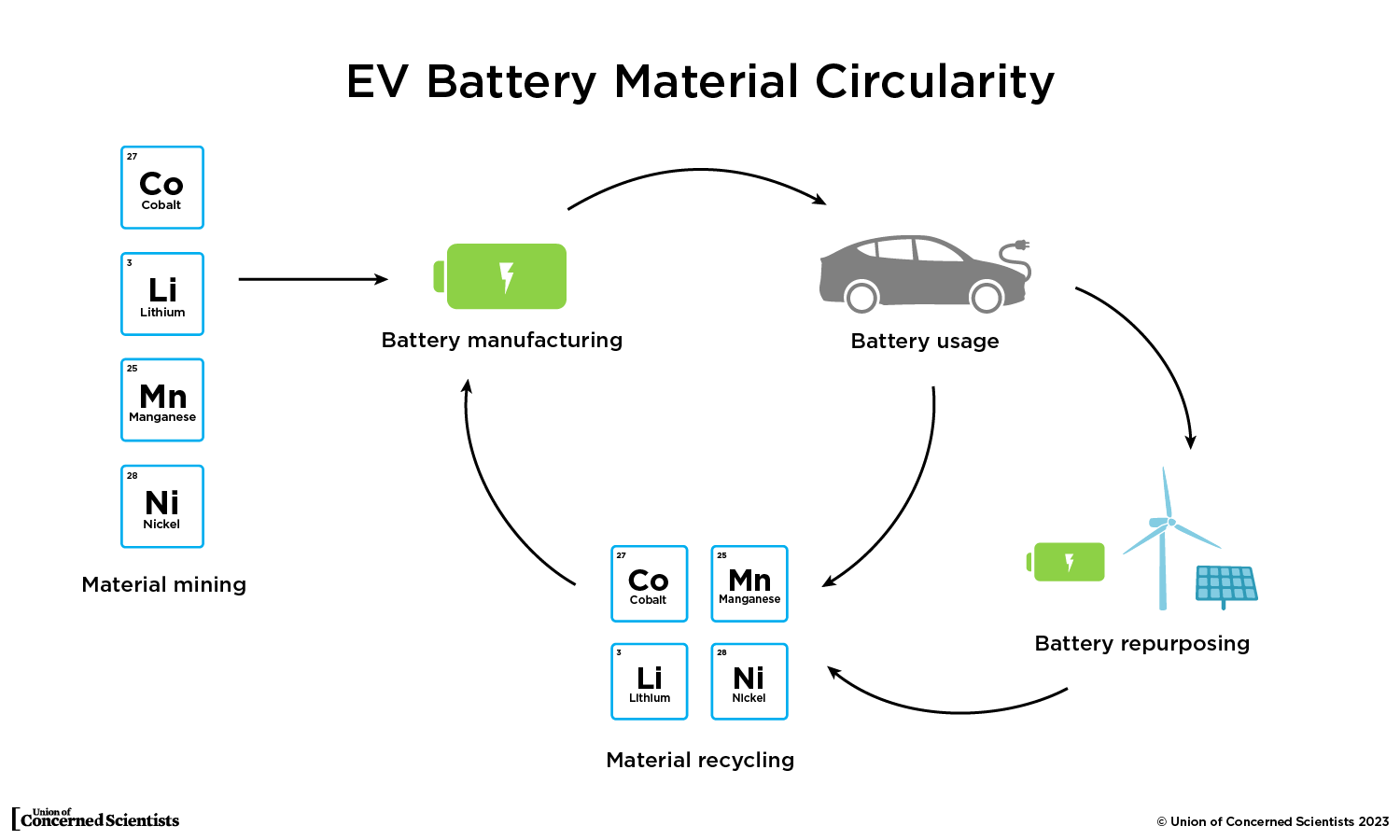
Battery policy agreed upon in the European Union implements circular economy principles and is the most ambitious battery policy to date. It has the potential to increase the recycling of batteries and the use of recovered materials through extended producer responsibility and recycling requirements. In the US, California is also exploring recycling and material circularity policy. In 2022, a report was released by the California Electric Vehicle Battery Recycling Advisory Group which outlines policies the group believes the California legislature should implement.
Policies discussed and proposed by these groups have the potential to increase the reuse, repurposing, and recycling of batteries, as well as mitigate impacts associated with end-of-life processes and increase battery sustainability. As policies develop, we at the Union of Concerned Scientists have outlined the following high-level principles that we will use to guide our policy positions.
Guiding principles
- Increased battery recycling and material circularity is necessary for a sustainable battery industry.
- The producer (in most cases, the vehicle manufacturer) should be responsible for ensuring EV batteries are reused, repurposed, and eventually recycled.
- The battery recycling process should minimize environmental impacts and have a high rate of material recovery, especially for lithium, nickel, and cobalt.
- Prior to recycling, the battery should be reused, refurbished and/or repurposed, if it is safe and has remaining capacity.
- The battery end-of-life should be considered during the design of the EV.
- Information about the battery’s health over time should be accessible when the battery is in the vehicle and after its removal.
- Government funding should continue to support research and development of battery repurposing, reuse, and recycling.
Let’s dive into these principles a bit further
Increased battery recycling and material circularity is necessary for a sustainable battery industry.
Recycling EVs already on the road is the most sustainable way to source materials. Embedded in these batteries is a highly concentrated amount of minerals that can be recovered through recycling. Newer recycling processes report recovery rates of 95% and low pollution impacts. This is a substantially better alternative than incineration-based techniques which do not currently recover any of the lithium and do emit greenhouse gases and particulate matter.
Once recovered, these minerals can be used to manufacture new batteries, therefore reducing the need for new mining. Overall, the decreased mining can make EVs more sustainable and lessen the risk of mishandling through inadequate storage or landfilling.
The producer (in most cases, the vehicle manufacturer) should be responsible for ensuring EV batteries are reused, repurposed, and eventually recycled.
Currently, the United States does not require EV battery recycling. While recycling is occurring, there is the potential for market dynamics to not catch all retiring batteries, therefore leading to improper disposal. Some newer batteries aren’t using cobalt and nickel, which are traditionally the highest value minerals in EVs. This trend is beneficial because it results in lower cost and more environmentally friendly EVs. But on the flip side, the recycling of batteries without these minerals isn’t currently profitable.and therefore may not be recycled if there isn’t regulation requiring it.
One potential policy solution is to define a central party responsible, such as producers, for ensuring batteries are recycled. Defining responsibility can increase the recycling rate and incentivize planning and efficiency.
The automotive manufacturers are best suited for this position, following the typical policy structure called Extended Producer Responsibility (EPR). By centralizing responsibility to the automotive manufacturer, it not only ensures the battery is recycled, but also incentivizes the producer to design the battery and EV in a way that makes recycling easier and cheaper.
This has been implemented for EV batteries in the European Union and was proposed by the California Advisory Group (the report uses the term ‘producer take-back’). A type of extended producer responsibility is used for ensuring the recycling of several products in California, including mattresses, paint, and carpet.
The battery recycling process should result in low environmental impacts and have a high rate of material recovery, especially for lithium, nickel, and cobalt.
Mineral recovery through recycling old batteries is significantly cleaner than mining new materials, and it is important that policies maximize the environmental benefits of recycling. This can be done through required material recovery rates and environmental impact reporting. Technologies are advancing and several new recycling companies state a 95% material recovery rate. This best available technology should be used, and the use of incineration-based techniques that do not recover lithium should not be allowed.
Prior to recycling, the battery should ideally be reused, refurbished and/or repurposed, if it is safe and has remaining capacity.
Eventually, all batteries should be recycled. But prior, many batteries can be used in the environmentally advantageous second-life application such as reuse, refurbishing, and repurposing. Reuse and refurbishing refer to reusing batteries in the same application, but in a different car. Repurposing refers to using the battery in a different application, such as for stationary storage to support renewable energy generation. Read this excellent blog if you would like to learn more.
The battery end-of-life should be considered during the design of the EV and the battery.
When an EV is retired, the battery is removed from the vehicle and then typically further disassembled. If the disassembly is planned for during the design of the EV and the battery, the process can become safer and more efficient. Examples of potential deconstruction process improvements through EV and battery design includes the use of binders instead of adhesives and standardization among pack design. Disassembly is currently a manual process, but if batteries are standardized and built to be taken apart, smart robots could instead do this job.
If extended producer responsibility is established, design for disassembly and recycling is naturally incentivized.
Information about the battery’s health over time should be accessible when the battery is in the vehicle and after its removal.
The battery health refers to the capacity and efficiency of the battery, something that slowly degrades over time and with use. This indicator is typically represented as a percentage and communicates the battery’s percent maximum available capacity in comparison to when the battery was new. It is important for EV owners to know the health of their battery, an indicator that is required starting in 2026 for EVs in California.
It is also important for battery health to be accessible once the battery is removed from the car. The battery health is a key determinant in deciding if the battery should be reused, repurposed, or sent directly to recycling. If the battery is in good health (i.e. relatively high capacity and efficiency), it should be reused or repurposed for a second-life prior to recycling.
Currently, if there is no visual damage, battery repurposers test the health by monitoring it through a complete charge and discharge or a specially designed testing process. This is expensive and time-consuming, but if this information was provided without extensive testing, repurposing can be expedited, and costs reduced.
Government funding should continue to support research and development of repurposing, reuse, and recycling.
As we transition away from the gasoline vehicle to the more environmentally friendly EV, battery recycling and material circularity should be priority. As discussed in a prior blog, there have been funds dedicated towards recycling research, development, and demonstration. While this funding is essential to developing a more sustainable battery industry, we also need policy that requires and ensures a circular battery economy.
What’s next for battery recycling policy
At UCS, we want to see that all EV batteries are safely recycled and the materials recovered are used in the manufacturing of next generation batteries. These materials are an essential part of meeting upcoming demand and decreasing the need for mining.
US policy should follow the example of the European Union by implementing extended producer responsibility, requiring high material recovery rates, and increasing access to battery information. Stay tuned for more blogs that dive into these principles.