The wind is in our sails on the voyage towards a clean energy future. Wind energy is currently the largest renewable energy source in the US, and the industry is growing fast. Wind energy companies have a strong commitment to ensuring the sustainable, responsible life cycle of their turbines and are progressing towards achievement of fully circular supply chains. To understand what that supply chain looks like, check out How Wind Turbines are Made, and for a deep dive into wind turbine blades, read “What Happens to Wind Turbine Blades at the End of Their Life Cycle?“
One component of wind turbines that I haven’t explored yet are the small but mighty rare earth elements. Rare earth elements, or REEs, are important parts of a wind turbine’s permanent magnets, located in the center of the blades in the electrical box (called the nacelle). The permanent magnets are mostly used to increase power generation and reduce maintenance in larger offshore wind turbines. Seventy-six percent of offshore and 32% of land-based wind turbines currently use rare earth permanent magnets.
The most common type of magnets used in wind applications are neodymium–iron–boron magnets (NdFeB). These magnets typically contain four rare earth elements: neodymium and praseodymium strengthen the magnet, while dysprosium and terbium make it resistant to demagnetization at high temperatures. The World Bank predicts that the demand for neodymium for energy technologies in 2050 will be 37% of total 2018 neodymium production. Global demand for neodymium for wind turbines is estimated to increase 48% by 2050. Rare earth elements are critical to the renewable energy future and are the main “critical metals” used in wind turbines. Sourcing them also involves social and environmental supply chain concerns.
Let’s dive deeper, then explore solutions for ensuring a circular rare earth element supply chain for wind turbine generators.
But first, a chemistry break!
Overall, rare earth elements include 17 elements of the periodic table. Famously, their name is a misnomer. They are not “rare”; they are as plentiful in the Earth as copper. But they rarely clump together for easy extraction, and when they do, it’s often highly concentrated in one place.
Our modern technological world wouldn’t function without rare earth elements. In essential yet miniscule quantities, they are like little alchemical superheroes, fueling almost every device that powers our digital lives. Before diving into their renewable energy applications, some fun facts:
- 4 of the 17 rare earth elements were discovered in Ytterby, Sweden. That place rocks!
- Promethium. Can you guess its namesake? The Greek Titan Prometheus who brought fire to humans. It is used to make luminous paint.
- The meaning of the name “Dysprosium” is “hard to get.” This element’s dating app bio writes itself!
- 12 of the rare earth elements are used in laser technology.
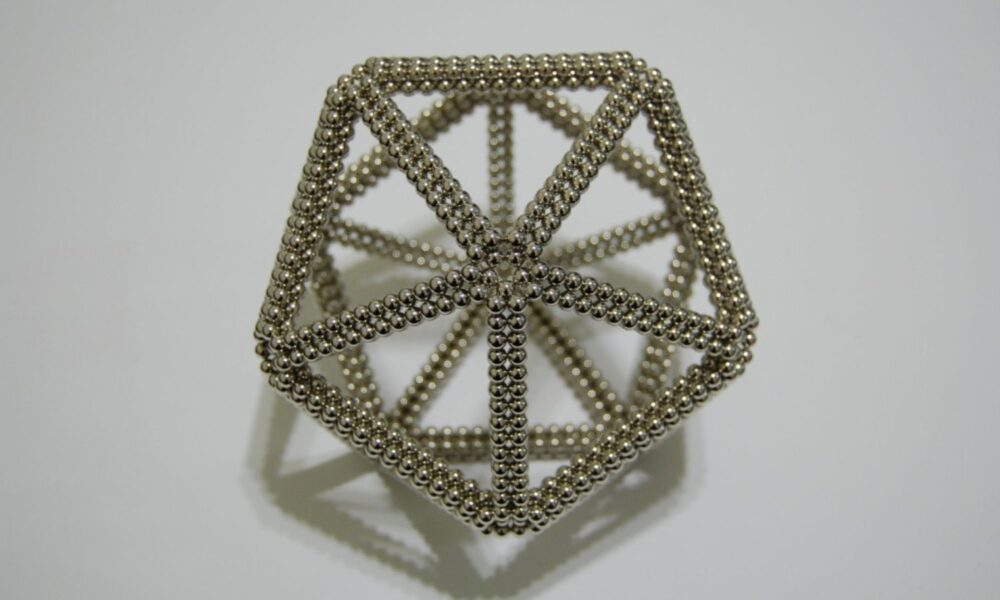
Mining rare earth elements
Rare earth elements help the gears of the wind energy industry turn. However, mining rare earth elements in large quantities is challenging, and the world needs more to satisfy growing demand. According to a 2020 Joint Research Centre report, assuming achievement of 100% renewable energy by 2050, along with increasing demand for rare earth elements from other sectors and only small improvements in technology, terbium demand in 2030 could slightly exceed projected supply, praseodymium demand could reach more than 175% of supply, and neodymium and dysprosium demand may exceed 250% of anticipated supply.
Mining rare earth elements can also involve serious human and environmental health threats. The fluoride and arsenic unearthed through rare earth element mining can cause lower birthrates and cause diseases such as skeletal fluorosis, which causes deformation in bone structure. In Baotou, Inner Mongolia, 1 in 7 Baotou residents—a city of several million—has cancer. A large rare earth element waste lake is located twenty minutes from the city center.
In 2010, China was producing 95% of rare earth elements, but since 2016 has decreased rare earth element mining down to 60% of world production today. Fifteen percent of rare earth elements are produced in the US, and 9% in Myanmar, where mining—particularly unregulated, illegal mining—has been increasing since the military coup in 2021. Kachin-based environmental groups estimate that there are over 100 rare earth element mines in the Pangwa and Chipwe Townships, owned by Myanmar military-affiliated militia. Radioactive waste from the mines pollutes the soil and waterways of dozens of nearby villages. A Pangwa activist told Radio Free Asia earlier this year, “These miners usually clear the ground and then dig holes. After that, they pour in chemically treated liquid into the holes. When they are done, they don’t cover up the holes in the ground, causing landslides when the rains come.”
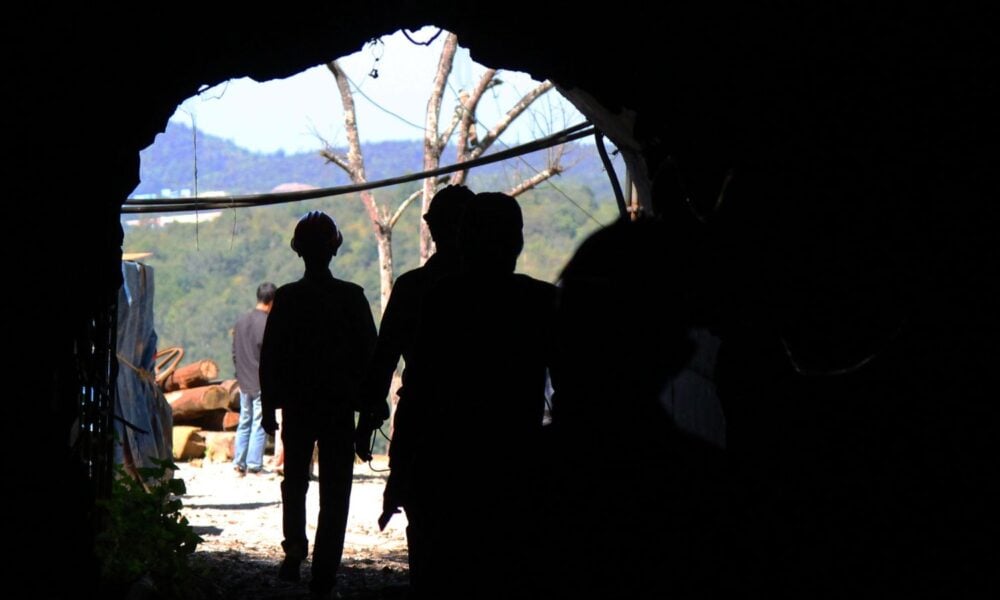
Recycling rare earth elements
Sourcing rare earth elements ethically and sustainably represents a big challenge. Many governments, the mining industry, and renewable energy companies are committed to tackling it. In addition to increasing oversight and transparency into rare earth element supply chains, one of many viable solutions to mitigating rare earth element extraction is recycling permanent magnets.
Today, the world recycles a small amount of rare earth elements from end products, but recycling could help meet the need of about 30% of future neodymium, praseodymium, and dysprosium demand.
Recycling of rare earth elements is currently accomplished through a combination of processes, including hydrometallurgy (acid leaching to extract rare earth oxides and salts), pyrometallurgy (roasting and melting at high temperatures), or electrochemistry (using electricity to separate materials based on their differing abilities to gain or lose electrons). A few companies–including Noveon Magnetics and REEcycle in Texas, as well as HyProMag in the UK–are early entrants to the rare earth element recycling space. Alternatively, the UK-based REEgain project is experimenting with using bacteria and microorganisms to absorb rare earth elements from products.
Solutions for a more sustainable, responsible, and circular life cycle
Even with continued research into substitute materials, the renewable energy future is likely to involve lots of rare earth elements. Sourcing them as sustainably, ethically, and circularly as possible is, and must be, a priority for the clean energy industry. Stakeholders from governments, to industry, to consumers can support strategies such as
- Ensuring ethical supply chains. Wind industry companies and their suppliers can join international councils for rare earth element ethical accountability, including the International Council on Mining and Metals and the Institute for Responsible Mining Assurance. They can ensure that their rare earth elements come from areas where nearby communities have provided free, prior, and informed consent to mining operations.
- Supporting rare earth element recycling. Governments can invest in research and development of rare earth element recycling and repurposing technologies by expanding recycling funding for entities such as the Department of Energy Critical Metals Institute, or providing competitive grants and start-up funding for recycling companies. Companies can also label their permanent magnets with the chemical compositions they contain, to facilitate safer and simpler disassembly and separation.
- Investing in rare earth element substitutions. Designing lightweight, powerful magnets with no or reduced neodymium, dysprosium, praseodymium, and terbium has been an elusive challenge for engineers. But they push onward, making progress with magnets based on cerium and cobalt and other materials. Some engineers also argue that other smart innovations regarding other aspects of the wind turbine design could reduce the need for REE magnets.
Rare earth elements aren’t technically “rare,” nor are the creative solutions for sustainable sourcing. Couple those bright ideas with circular wind turbine blade solutions, and we’re jetting towards a circular wind turbine life cycle!
How are wind turbines made? What happens when wind turbines reach the end of their service lifetimes? Where do their raw materials come from, and when they retire, can we process those materials into other useful products or recycled blades? How can we move towards a sustainable, responsible wind energy supply chain, and ensure all materials come “full circle”? Click the links below for answers:
What Happens to Wind Turbine Blades at the End of Their Life Cycle?
Are you also curious to learn about the life cycle of solar panels? Read on:
Mining Raw Materials for Solar Panels: Problems and Solutions